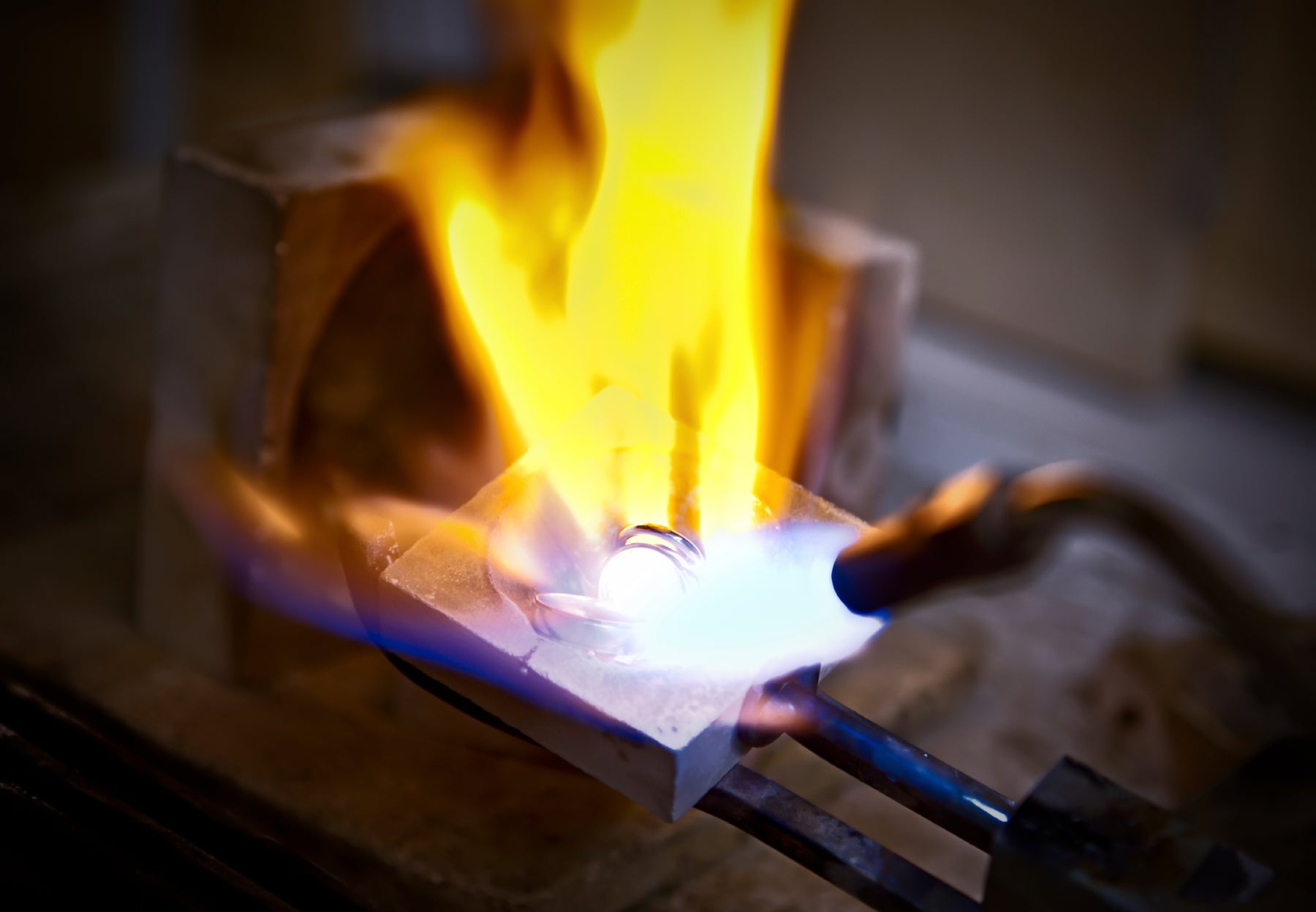
Palm Coated Work Gloves – Polyurethane vs Foam Nitrile Coating
Palm-coated work gloves are suited for handling small parts, the automotive industry, metalwork, fabrication, construction, the food industry and general purpose. Palm coatings bring important benefits and options to work gloves, including enhanced grip, higher levels of abrasion resistance, and even water resistance. But choosing the correct glove coating for your job can be tricky. This article will compare the two most popular types of glove coatings: polyurethane (PU) and foam nitrile.

Polyurethane (PU)
If you’re looking for a glove coating that’s extremely flexible, relatively inexpensive, and has a low particulate shed, polyurethane Palm-coated work gloves (PU) gloves are a good choice. While not the most durable coating, polyurethane will provide a phenomenal grip without ever feeling sticky.
Unlike nitrile glove coatings, synthetic polyurethane offers a high level of breathability along with dexterity. This sort of coating will enhance puncture resistance while maintaining the ever-important tactile sensitivity. A polyurethane coating will help you to maintain the necessary dexterity you need when performing fine motor tasks and this type of coating offers a more “bare hand” grip because the coating has a tacky feeling which would be appropriate which works excellent for dry conditions but not well in wet or oily conditions.
Polyurethane’s (PU) softness, combined with moderate puncture and abrasion resistance, make it a most versatile polymer. Polyurethane coating offers great stretch, strength, and low particulate shed.
Chemically, polyurethane has excellent resistance to oils, solvents, fats, greases, gasoline, oxidation and ozone but has poor resistance to hot water and is not recommended for use above 79°C.
The low-particulate shed mentioned earlier make PU Gloves a perfect choice for those working with electronics, manufacturing, small parts handling and cleanrooms.
Foam Nitrile
High Visibility Safety Glove
For those who work in oily and wet conditions on a regular basis, gloves with foam nitrile coatings are unparalleled in the workplace. Nitrile provides excellent comfort and dexterity and when foamed, it behaves like a sponge by soaking up oils and liquids and displacing them, leaving the wearer with improved gripping capabilities. Foam nitrile is known to provide these super grip levels when dealing with any sort of moisture and in those situations, is able to create a suction cup effect which significantly enhances grip.
To a reasonable extent, Foam Nitrile-coated gloves are also puncture, cut, snag, abrasion, oil, fuel, and tear resistant – three times more puncture resistant than rubber. Nitrile isn’t flame resistant, but does well in a range of temperatures: between -4°C (25°F) and 149°C (300°F). Foam Nitrile gloves are a good choice for jobs working with oily parts like in metal stamping and mechanics.
Based on these key features of each type of coating, the best rule of thumb is to use foam nitrile in wet conditions and polyurethane for dry conditions.
Smith & ARROW sell a variety of PU and Foam Nitrile Industrial Gloves in all sizes, including Hi-Vis, Touchscreen and our variant Sandy Nitrile Cut Resistant (Level 5) options.
What Safety Work Glove Ratings Mean
All Smith & ARROW Work Gloves are have EN388 Certification giving a measured protection from mechanical risks across 4 industry parameters: Abrasion, Cut, Tear, and Puncture resistance – each rated from lowest “1” through to highest “5”. Protection against mechanical hazards is expressed by a pictogram followed by these four constructs (performance levels), each representing test performance against a specific hazard.
1. Resistance to abrasion
Based on the number of cycles required to abrade through the sample glove (abrasion by sandpaper under a stipulated pressure). The protection factor is then indicated on a scale from 1 to 5 depending on how many revolutions are required to make a hole in the material. The higher the number, the better the glove.
2. Blade cut resistance
Based on the number of cycles required to cut through the sample at a constant speed. The protection factor is then indicated on a scale from 1 to 5.
3. Tear resistance
Based on the amount of force required to tear the sample. The protection factor is then indicated on a scale from 1 to 5.
4. Puncture resistance
Based on the amount of force required to pierce the sample with a standard sized point. The protection factor is then indicated on a scale from 1 to 5.
Smith & ARROW sell a variety of PU and Foam Nitrile Industrial Gloves in all sizes, including Hi-Vis, Touchscreen and our variant Sandy Nitrile Cut Resistant (Level 5) options.